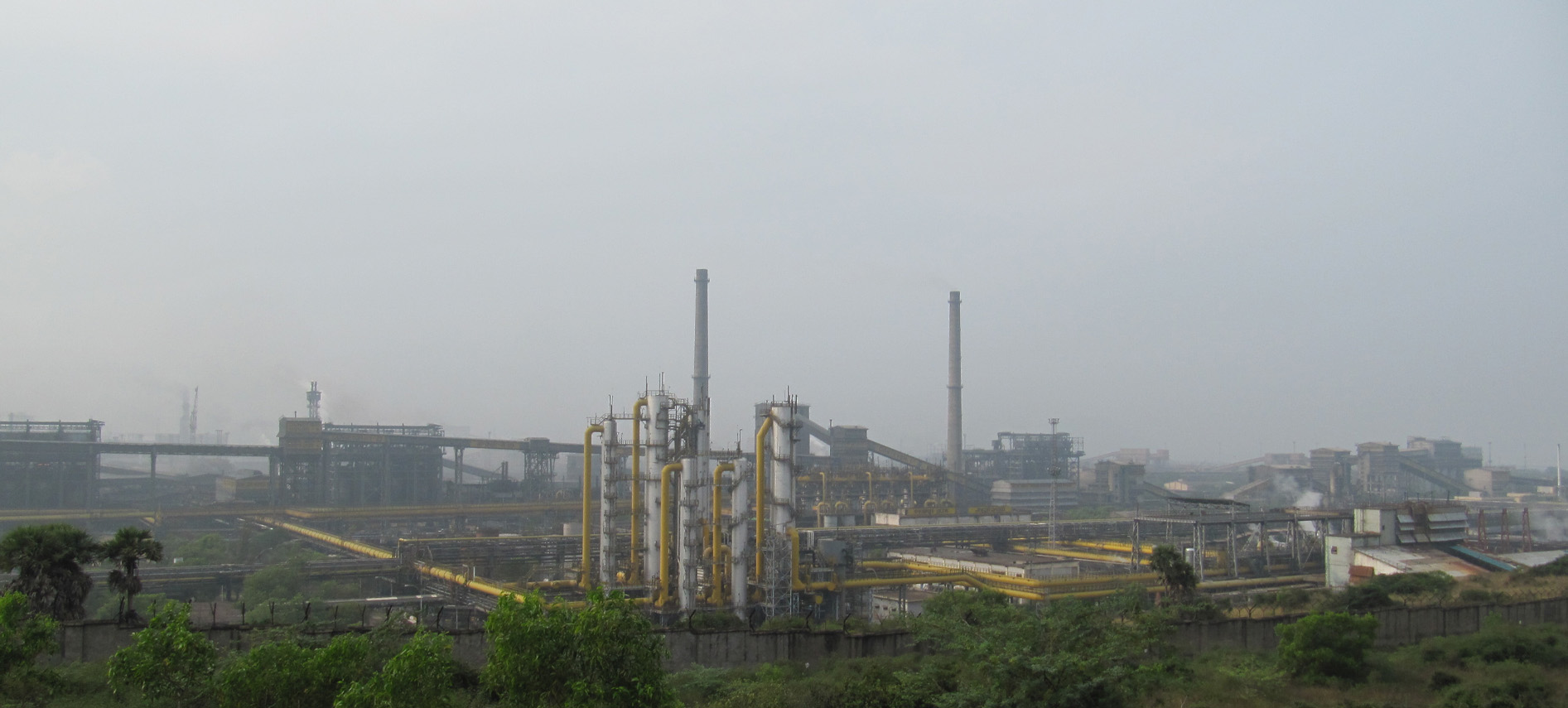
Sinter plant №3 construction with capacity rating to 3.611 MTPA of sinter with sintering area of 408 m2.
The construction is being performed within frames of the Steel Plant expansion program with increase of capacity up to 6.3 MTPA of steel.
Sinter Plant is to provide Blast Furnace № 3 of 3200m3 volume commissioned in 2013 with sinter. The construction is being performed on “turn-key” basis in conformity with the Contract, signed on the results of tender dt. 01.05.2007 between Visakhapatnam Steel Plant and the consortium consisting of JSC “VO “Tyazhpromexport”, Russia (the Leader) and McNally Bharat, India (the supplier of Indian equipment and services).
The Customer Consultant is the M.N.Dastur and Co.(P) Ltd. company, Kolkata, India. JSC “VO “Tyazhpromexport” scope of work includes the supply of the Design & Engineering and the main technological equipment, supervision and management of the construction, erection, tests, start up and commissioning of the Project as well as Indian operating personnel training.
Subcontractors of JSC “VO”Tyazhpromexport” are as under:
The State Enterprise “UkrGipromez”, Dnepropetrovsk, the Ukraine, the General Designer of the Sinter Plant;
JSC “Heavy Engineering ORMETO-YUMZ”, Orsk, Russia –the designer and the supplier of the sintering machine, mixer , nodulizer and crusher;
“Siemens Vai Metals Technologies Gmbh & Co.”, Linz, Austria –the designer and the supplier of the ring cooler;
“Howden UK Ltd.”, Belfast, England – exhauster supplier;
“Tecno Vibrazioni Venanzetti”, Milan, Italy – the supplier of sinter screens.
The main guarantee parameters are the following:
Daily average output (within 3 days) – 10 950 t/24h
Max. output (within 24 h) – 13 190 t/24h
Consumption of mixed gas – not over 15000 Kkal/t of sinter
Fuel consumption – not over 60 kg/t of sinter
Dust emission into the environment at exhaust outlet – not over 50 mg/nm3
Dusting in the working area – not over 5 mg/nm3
Noise level 3 m from equipment – not over 85 decibel
Equipment erection was completed in 2013. Obligations fulfillment under the Contract inclusive of the guarantee period of 12 months is planned for 2015
2-nd grade repairs of Blast Furnace №1
Blast Furnace №1 (BF-1) with volume 3200m2 rating hot iron output to 1.7 MTPA was constructed according to the design of LenGipromez and commissioned with technical assistance of JSC “VO “Tyazhpromexport” in 1990.
In view of the 2-grade capital repair planned for 2000 and in conformity with the Contract signed with JSC “VO “Tyazhpromexport” on 24.5.1997 technical & design documentation was developed and handed over to the Customer for conducting the repairs.
In April, 2000 in accordance with Contract № 44-189/02500 dt. 14.7.1999 JSC “VO”Tyazhpromexport” performed supplies and executed works on 2-nd grade capital repairs of Blast Furnace №1 “on turn-key” basis.
In course of capital repair cooling plates were replaced till the bosh zone and partially lower the bosh zone, carbonaceous blocks of the part of hearth side walls, refractory lining of the stack and bosh zones, defective furnace shell sheets and so on. The works were performed without considerable changes of the main furnace design.
Maintenance time (taking into consideration the replacement of 3 rows of hearth bottom carbonaceous blocks) – 49 days.
Subcontractor of VO”Tyazhpromexport” under preparation of repairs documentation, equipment supplies and execution of repairs works was JSC “Centredomnaremont”, Tula, Russia.
2-nd grade capital repair of Blast Furnace №2
Blast Furnace №2 (BF-2) similar to BF-1 as per volume (3200 m3) and output (1.7 MTPA of hot metal) was commissioned in 1992.
2-nd grade capital repair of BF-2 under Contract № 44-180/08500 dt. 20.10.2000 was made by JSC “VO”Tyazhpromexport” in 2001 using “know-how” and technical documentation, haven been used for the capital repair of BF-1.
Maintenance time (taking into consideration the replacement of 2 rows of hearth bottom carbonaceous blocks) – 38 days.
The subcontractor of JSC “VO”Tyazhpromexport” – JSC “Tsentrdomnaremont”